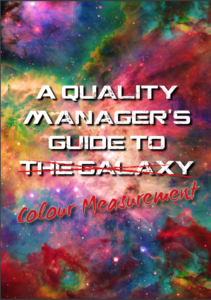
Why is measuring the colour of your plastic pellets, masterbatch, resin and recycled material important?
Simply put, analysing, quantifying and putting meaningful numbers to the physical appearance of your plastic pellets, masterbatch, resin and recycled material will allow for quality control checks that can monitor the overall efficiency, consistency and accuracy of your manufacturing processes.
With these quality control checks, any sub-standard or out of specification, plastic pellets can be identified immediately and the cause rectified before a great deal of money is lost in unusable product, staff hours spent reworking and wasted materials.
There are certain appearance anomalies that can instantly indicate an issue with the product and therefore its production method.
For example, with plastic pellets, there should be a consistent colour, the presence of particles of a different colour is normally an indicator of an issue during the manufacturing process. Differing colours can be the result of impurities in the ingredients/materials and the presence of contaminants. This also includes the process running to fast, too slow or too hot.
Monitoring the colour of the product over time can also be an indicator of the condition of the product as it ages. This indicator is an asset to quality control when conducting shelf life analysis.
The main aim of colour and appearance analysis and measurement is to be able to monitor the effectiveness and reliability of the manufacturing process and identify any areas that may need improving. By addressing any issues, you can guarantee the manufacturing process will result in products of high quality and generic appearance, consistently.
Not monitoring the appearance of your plastic, pellet, process can result in lost revenue, annoyed customers and a headache in re-working the process.
If an extruder cannot get consistent blends and formulations from you it could ultimately cost them thousands in drifting products and the main goal here is to keep the cross charges to a minimum.
Do your colour complaints and cross charges cost your company more than £20k a year? Could your products appearance be shifting out of tolerance?
Stotto Specialist Sensors has a solution for you. We can implement a system to set boundaries and specifications so both you and your customers know what to expect.
Our service will provide you with the tools to prevent out-of-specification products and vastly reduce customer returns, not to mention help you optimise and make savings on your production process.
The HunterLab ColorFlex EZ is a 45/0 Spectrophotometer capable of measuring a variety of plastic products accurately and providing easy-to-understand appearance data that you can use to streamline your quality control processes and set product specifications, giving you the peace of mind that the customer is only receiving the very best.
To measure the quality of your production processes, simply fill a sample cup with your product, place on the instrument and start measuring. The HunterLab ColorFlex EZ will take an average measurement of your sample and provide you with the data to let you know how good your product really is, visually.
OPTION 1
£12,437.22 (plus local tax where applicable)
Includes:
Instrument
Delivery to a UK or Irish address
Award winning remote technical installation and method training
OPTION 2
£15,810.22 (plus local tax where applicable)
Includes:
Instrument
Delivery to a UK or Irish address
On-site technical installation with method and application development (method implementation and money saving included)
2 year service agreement
Resources and documents from our knowledge base you may find useful
Stotto
3 Meer End,
Birstall,
Leicestershire.
LE4 3EH
Stotto 2024 | Terms, Conditions & Useful Information | Privacy Policy | Site Map